Dielectric Testing Equipment for Bucket Trucks
Dielectric testing is crucial for the long-term maintenance and safety of bucket trucks. Not only is this a standard way to check the voltage capacity of bucket truck insulation materials, but the correct application of the test can check for damaged materials as a way to prevent an accident.
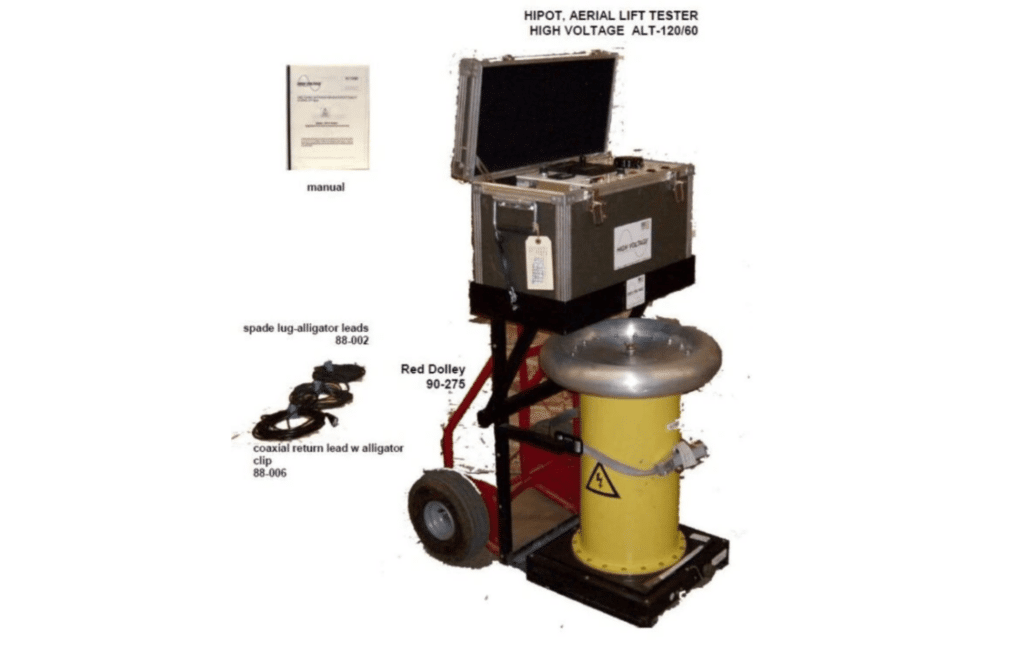
Source: https://jmtest.com
By performing insulation resistance testing according to OSHA and ANSI (the Occupational Safety and Health Administration and the American National Standards Institute) standards, not only do you protect your employees and team members working with bucket trucks, but you also catch potential condition issues outside of operation hours.
Hipot Testing
Thankfully, there is standardized dielectric testing equipment made to measure the power and leakage current of insulation materials. Dielectric testing equipment, called hipot or hi-pots as a shortened form of high-potential or high-voltage, sends a controlled burst of output voltage to properly test insulation resistance and check for any issues that contradict applicable safety standards.
This equipment can operate using DC (direct current) or AC (alternating current). You will need a different hipot device for different tests, as different materials have specific requirements for dielectric testing standards.
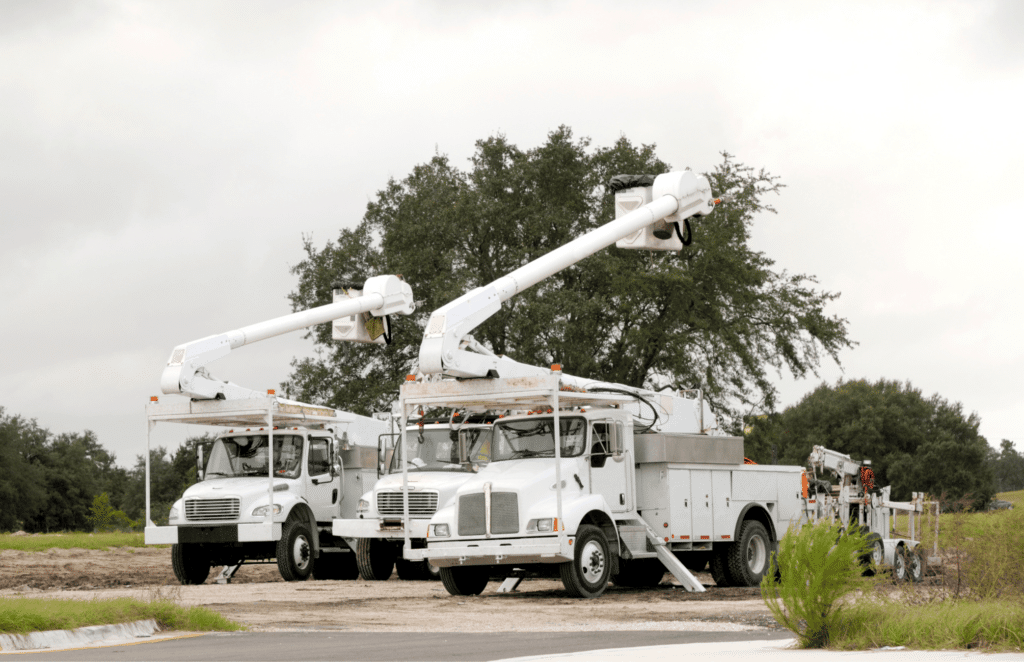
Hipot testing requires the application of high electrical currents to insulated materials. The hipot has the right software to capture the electrical insulation resistance measurement, allowing certified testers to tell the properties of the materials during the inspection. There are two types of dielectric tests that this can apply to:
- the dielectric strength test, which determines how high the voltage can get before the material allows it to flow,
- and the dielectric withstand test, which is how long materials can hold a current before they break down.
The testing focuses on three major categories:
- Oil Spectro-Analysis (for insulating oil)
- Stability Test (for physical integrity)
- Thickness Test (thickness of different mechanical parts)
One reason a manual inspection is necessary for testing equipment is that it enables testers to detect flaws in the insulation materials. There is a wide range of flaws that can pose serious threats to bucket truck operators, which is why routine inspections are crucial, even outside of hipot testing regimens. Not only are they crucial for safety, but ignoring these regulations is illegal and can come with a heavy fine, as well as other repercussions.
Equipment for Dielectric Testing
Shifting back to dielectric testing, hipots come in different voltage options and standards depending on what you’re testing. First, determine if you need AC or DC testing equipment, as that changes the kind of hipot you’re working with.
Secondly, it’s important to know what material you’re testing, as you may need higher voltage for different kinds of equipment. Since dielectric testing checks the integrity of several FRP (Fiberglass-Reinforced Plastic) parts of your bucket truck, different equipment may be needed for each part of the truck. Keep in mind that dielectric integrity tests check:
- Upper and lower booms
- Buckets
- Liners
- Differ derrick extensions
- Tool Circuits
- Upper control systems
Of course, these pieces of equipment vary depending on what kind of bucket truck you have, so it is normal for your bucket truck to not require everything on this list depending on its tools.
Boom Testing Equipment
Boom testing is often the first thing people think of when they think of bucket truck insulation testing. After all, this lift is at a crucial juncture, carrying a worker often near power lines and other sources of potential electric currents. Testing the insulation of the boom materials is crucial, especially as the truck ages. Age can greatly impact the insulation capacity of a material, meaning routine dielectric testing according to ANSI standard 92.2 is critical for the long-term safety of a bucket truck.
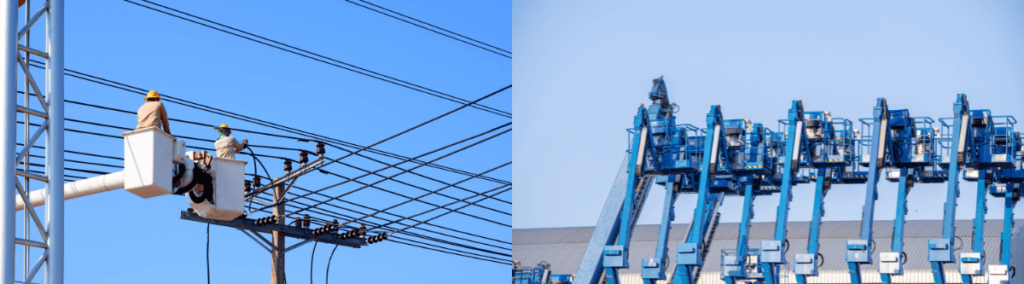
For example, a 0 – 100 kVdc @ 10 mA for DC testing and a 0 – 120 kVac model for AC voltage testing is usually standard for a normal insulated boom truck. However, a heavily insulated boom truck may require a 200 kV – 400 kV AC or DC. Because of the power discrepancies between different hipot voltages, it’s important to follow all manufacturer and safety guidelines when choosing the right hipot device for testing. It’s worth noting that boom testing requires the highest voltage but the lowest current. This is because the capacitance (the capability of a material object or device to store electric charge) of the boom is relatively low.
Liner and Tool Testing
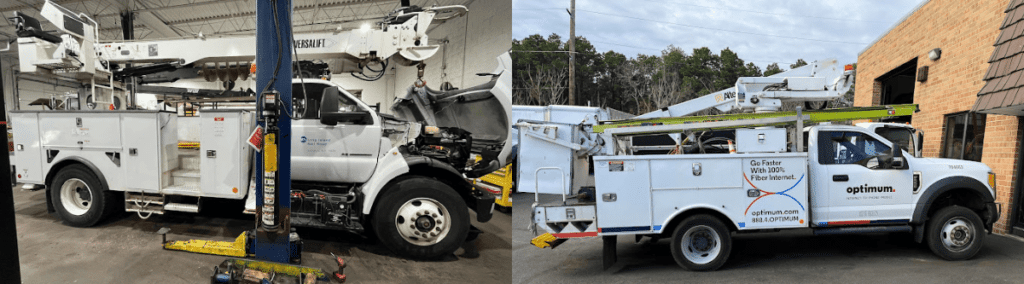
It is worth noting that dielectric testing is not just for the boom of a bucket truck. Liners and workman’s tools must also be tested for conductivity to ensure total safety. With tools and liners, AC is usually used, as this is the most common current workers run into on the job. To test liners with AC, 0 – 50 kVac hipot is needed, though water bath liners have a higher requirement, needing 9 – 10 kVA of power. This means a specialized hipot test may be needed for double-liners.
Oil Dielectric Testing
If you’re unfamiliar with insulating oil, you may be unaware that this substance requires routine dielectric testing. Not only is insulating oil important for insulation, but it also acts as a coolant, providing necessary cooling functions during the operation of bucket trucks and other insulated vehicles. Insulating oil loses its effectiveness under certain conditions, including age and moisture content, so it’s important to regularly check the health of insulating oil to stave off these issues.
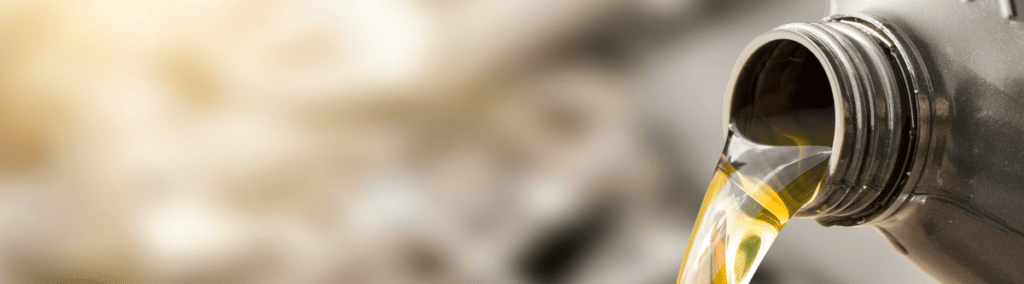
In fact, it could be argued that dielectric testing of insulating oil is one of the most common forms of maintenance and testing done on an insulated vehicle. For oil dielectric testing, you will need a 0 – 60 kVac oil dielectric tester. These testers are made to only test the oil itself, and as such are specialized compared to some of the other dielectric testers we’ve covered so far.
As you can see, there’s a wide range of specialized equipment needed for dielectric testing, meaning it’s best to work with a dielectric testing professional as they can not only test to industry standards, but also already have the needed equipment to test accurately and safely. Remember, it’s important to have your bucket trucks routinely undergo dielectric testing to ensure there’s no material decay or damage that could lead to electrical shock or even death.
Commonly Used Standards for Dielectric Testing Equipment
If you’re someone who works with bucket trucks and their safety requirements, you’re most likely familiar with ANSI Standard 92.2. However, in order to understand the various voltages used for dielectric testing, you also need to consult American National Standard Techniques for Dielectric Tests, C6B.1-196B. According to ANSI Standard 92.2:
“With electrodes as described in 4.11, tests shall consist of rated, double-rated, and at the manufacturer's option, either momentary withstand or switching surge voltage (see· footnote Table 1). The voltage is raised to rated voltage and the current recorded. The voltage is then raised to double-rated voltage and held for three minutes, recording the current at the start and end of the three-minute test period during which the current shall neither increase more than 10 percent nor exceed the values given in Table 1. The switching surge withstand test shall be in accordance with American National Standard Techniques for Dielectric Tests, C6B.1-196B, or the latest revision thereof.”
Since that’s a lot of internal referencing to consider, we’ve provided a copy of Table 1, which outlines the manufacturer’s guidelines for dielectric testing using dielectric testing equipment, which should be followed by dielectric testing facilities.
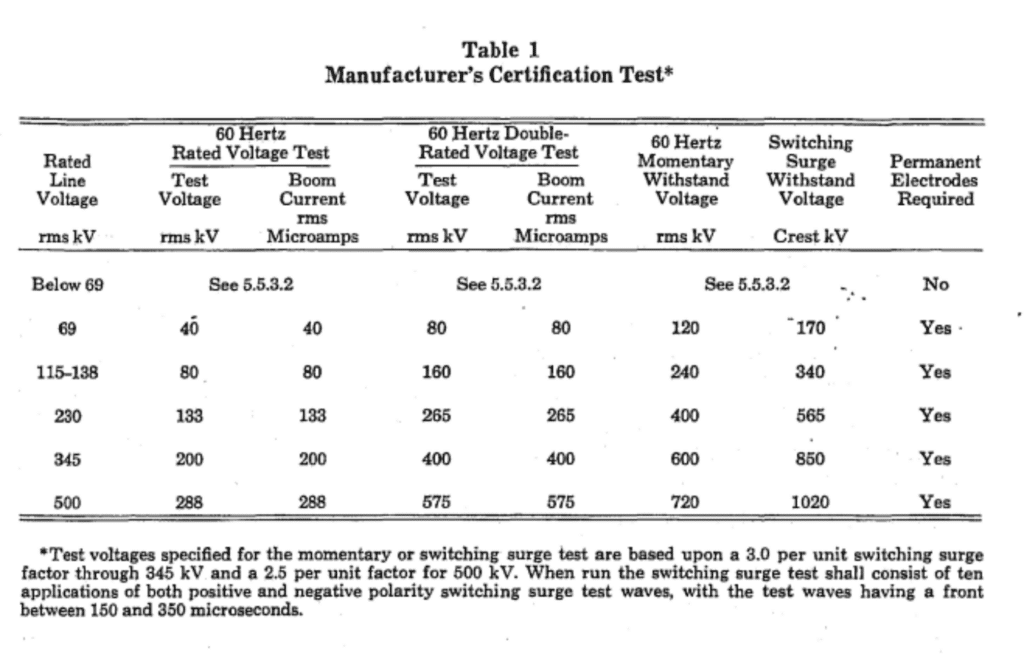
If you’re a layman, that’s a lot of information to process. Thankfully, companies like TCL Auto and Truck Repair Service Center are experienced with dielectric testing, so they know exactly where to place any nodes and how to read the hipot equipment correctly during testing. It is worth noting that our earlier outlines as to the strength of hipot testing equipment still applies to routine dielectric testing, so you can use those guidelines as an estimate if searching for dielectric testing materials for your company.
Choosing the Right Dielectric Test Equipment
Imagine you’re picking out a new smartphone. You wouldn’t just grab the first one you see; you’d look for one that fits your needs, right? The same goes for selecting dielectric test equipment for your boom truck.
- Consult a Certified Retailer: It's crucial to work with a certified retailer. They can guide you to equipment that can handle the electrical output needed for your truck's insulation.
- Diverse Equipment for Different Components: Just like you need different apps for different tasks on your phone, you need various types of hipot testers for different parts of the truck. For instance, the gear for testing insulating oil differs significantly from what's used for checking a boom at full height.
Remember, the goal is to have the right tool for every test, ensuring each component is safe and functional.
Maintenance and Calibration of Dielectric Equipment
It’s funny to think about the fact that the calibration equipment for dielectric testing requires its own calibration, but it’s true. Getting your dielectric equipment regularly calibrated between tests can ensure you’re getting the correct readings at all times, and don’t end up missing crucial signs of wear and tear on bucket trucks.
Thankfully, many companies that sell dielectric testing equipment also provide calibration options for their equipment. This means you can often either find someone who calibrates your equipment nearby, or ask your equipment provider who they recommend for calibration. Be sure to make a note of when your equipment was last calibrated and stick with a routine calibration schedule for best results.
Future Trends in Dielectric Testing
Trends point in a positive direction for dielectric testing. Not only is the constant innovation in this department but new machines coming out all the time to help challenge the industry and provide new standards for safety. Many scholarly articles point to the development of new testing protocols that don’t destroy underlying material to check its insulation capacity, which could revolutionize how dielectric tests for certain materials are done in the future.
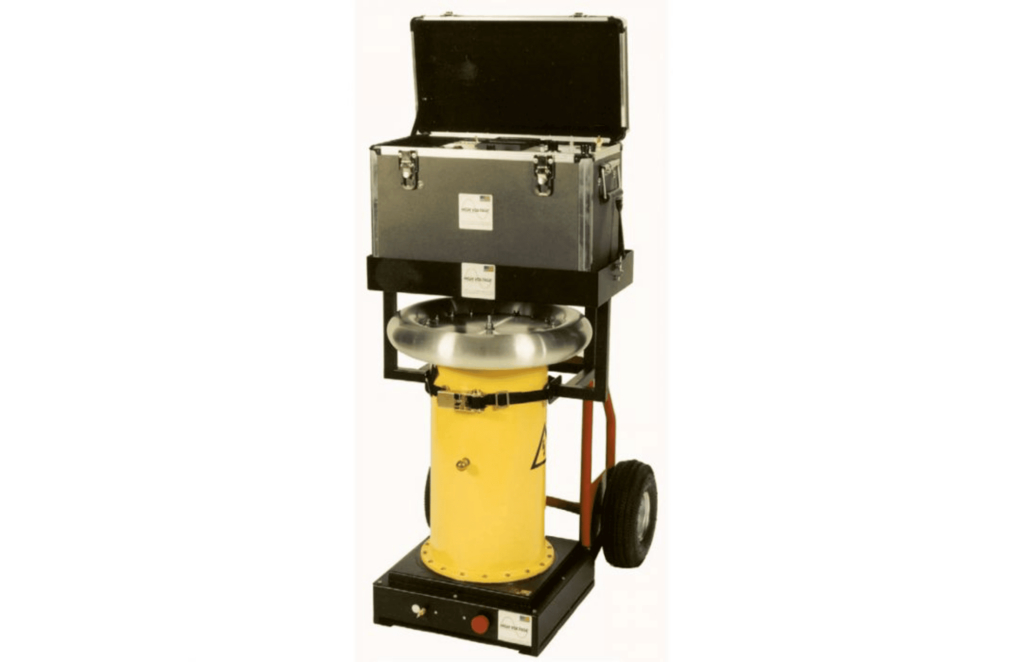
Since our understanding of electricity and insulation changes regularly, the dielectric testing requirements and equipment that matches those requirements are likely to change over time. It’s hard to estimate the exact changes coming to dielectric testing, but with current innovations taken into consideration it’s likely we’ll see a new set of standards and equipment in the next ten years, pointing to safer standards for dielectric testing and bucket truck development as a whole.
Frequently Asked Questions
What is a Dielectric Withstand Tester?
A dielectric withstand tester helps determine how long materials can survive under a set current. For example, if an insulating material is subject to high currents over time, how long can it withstand that current before allowing electricity through? This is crucial for the overall safety of bucket truck operators, as it helps determine how long an insulating material can last when exposed to higher-than-average currents.
What does the dielectric test for bucket trucks Include?
Dielectric integrity tests check:
- Upper and lower booms
- Buckets
- Liners
- Differ derrick extensions
- Tool Circuits
- Upper control systems
These tests also check the dielectric withstand rating of various insulating materials. By checking all equipment that is insulated, these tests ensure that workers stay safe while operating bucket trucks near sources of electricity.
How long does the inspection take?
Dielectric inspections are short. These tests can take anywhere between 10 to 60 seconds. Generally, a dielectric inspection takes only 10 minutes once set up, as testing electrical currents is faster than other inspections.
What happens after a Dielectric test?
After a dielectric test, you’ll find out if you need repairs done to your vehicle. This can include replacing insulation materials, or further tests. If you passed a dielectric test, you should mark down when the next test date is so that you can stay on top of your standard testing requirements.
Conclusion
Since so much specialized equipment goes into running a dielectric test, it’s always a good idea to work with professional testing centers like TLC Auto and Truck Repair Service Center. Our team can easily conduct dielectric tests for your vehicle, without you needing to invest in the inspection devices for yourself. If you have any questions about dielectric testing, don’t hesitate to reach out to our team to find out more, or to schedule a test today.